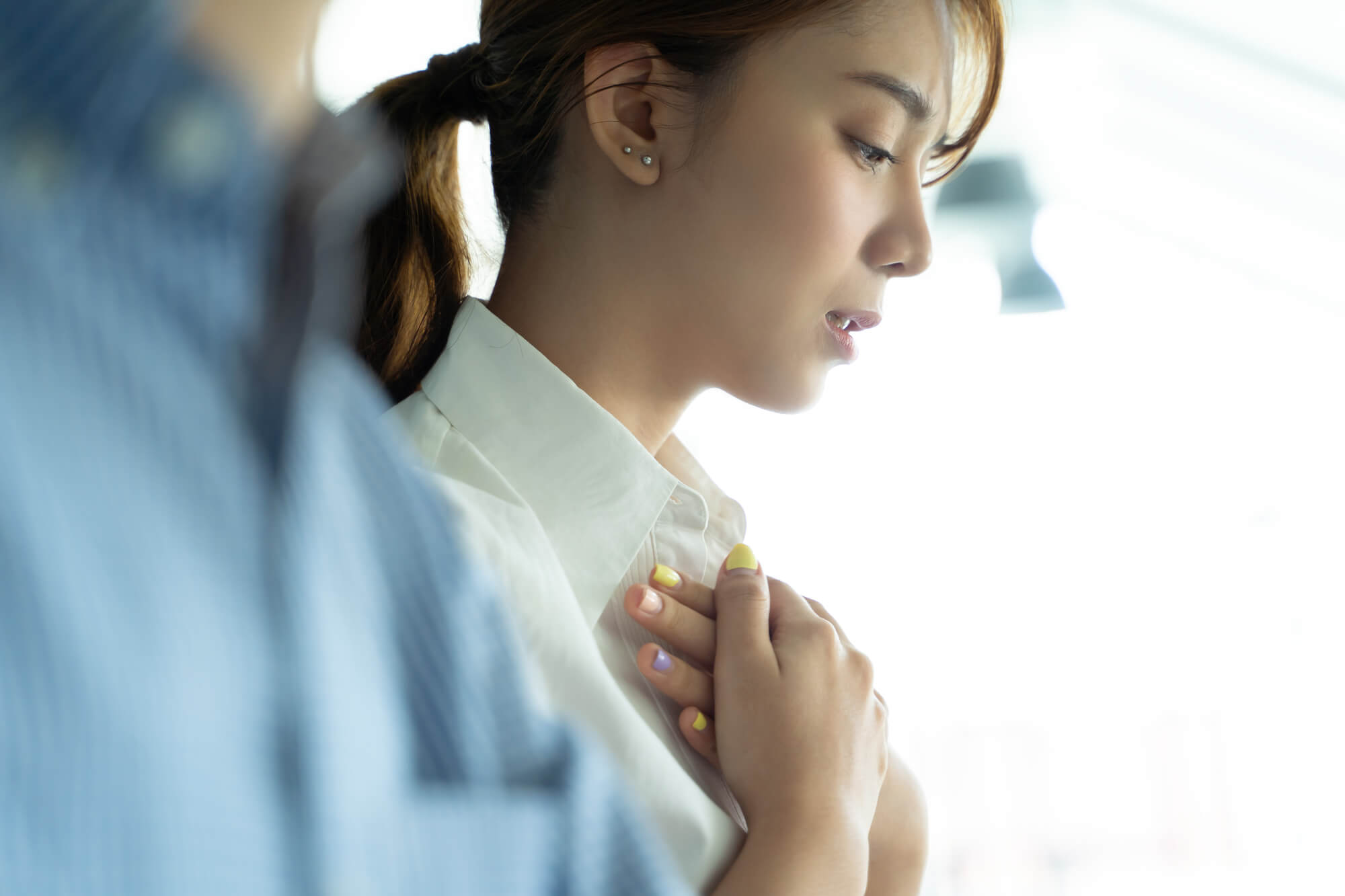
2025.02.20
2024.11.25
実務
製造業の現場では、作業の効率化と生産性向上が日々の課題となっています。現場の無駄をなくし、よりスムーズな業務運営を実現するためには、具体的な改善点に注目して、小さな改善点から取り組むことが大切です。
本記事では、工場における製造業務の見直しから、効率化を図る際のポイント、実際の改善策まで幅広く紹介します。工場の作業効率を最大限に引き出せる情報をお伝えしますので、ぜひ最後までご覧ください。
まずは、工場の製造業務の生産性向上やコスト削減を目指すため、注目すべき7つの改善策をご紹介します。
①
生産ラインや業務の可視化と見直し
センサーやIoTデバイスを導入し、ラインや工程を可視化して各プロセスをリアルタイムで計測することにより、特定の工程で問題が発生している箇所を正確に把握できます。
可視化させることで、ボトルネックとなっている部分を迅速に特定し、即座に改善することが可能です。また、フローチャートやデータ可視化ツールを使用し、業務の見直しを行うことも効果的で、工程全体の効率が向上して無駄を削減できます。
②
定型業務の自動化
デジタルツールや自動化システムを活用し、定型業務を自動化することで、発注や在庫管理、資料作成といった反復的な定型業務を効率化できます。結果、ヒューマンエラーや発注ミスを大幅に削減できるのです。
また、AIを用いて機械の運転時間やメンテナンス計画を最適化し、稼働率を向上させる方法も有効です。さらに、組み立てや検査作業の自動化が進むと、作業者の負担が軽減され、全体の生産性も向上します。
③
レイアウトの見直し
機械や作業工程の配置を見直し、材料や部品の受け渡しを円滑にすることで、移動時間や手間を削減できます。同じ工程が複数回必要な場合は、関連する機械を近くに配置することで作業効率を上げましょう。
適切なレイアウト設計は、無駄を省いた効率的な作業を実現させ、業務のスピードアップと生産性向上に役立ちます。
④
状況の可視化
在庫と生産の状況を可視化することも、効率的な製造業務を実現するためには欠かせません。状況の可視化により、不良在庫や欠品を未然に防ぎ、過不足のない生産体制を構築することが可能です。
なお、IoTやRFIDなどの技術や分析ツールを用いることで、在庫や生産の状態をリアルタイムで把握しやすくなり、迅速な対応ができるようになります。
⑤
運用管理を効率化
製造業の基幹システムには膨大なデータが蓄積されますが、そのデータを効果的に活用するためには運用管理の効率化が大切です。また、基幹システムの機能のみでは対応が難しい場合、外部ツールと連携することで、データ管理や分析がよりスムーズに行えるようになります。
外部ツールを効果的に活用し、迅速な意思決定や改善活動を実現させて、運用管理の効率を全体的に高めましょう。
⑥
部署間での連携を見直す
部署間の連携を改善することは、認識のズレや情報伝達ミスの防止につながり、業務の効率を大幅に向上させます。特に製造業においては、現場と他部署とのスムーズな連携が必要です。
社内での情報共有ルールの整備や定期的な交流会の実施、コミュニケーションツールの導入などにより、部門間の理解を深めることで、情報が円滑に伝わりやすい体制を構築できます。
⑦
「5S」の徹底
「5S」とは、製造現場における無駄をなくし、効率的で安全な職場環境を保つ5つの活動を指します。Sから始まる5つの言葉で成り立っています。
「整理(Seiri)」:不要物を排除し、必要なものを明確にする
「整頓(Seiton)」:道具や材料を使いやすい位置に配置し、作業のスムーズさを確保する
「清掃(Seisou)」:現場の汚れを除去しながら設備の異常も点検する
「清潔(Seiketsu)」:整理・整頓・清掃を継続し、清潔な環境を維持する
「しつけ(Shitsuke)」:これら4つのSを習慣化し、従業員全体に浸透させる
以上の5つを徹底することで、ミスや事故のリスクが軽減して作業効率も向上します。
ここでは、工場の業務効率化を図るため、具体的な改善策を考えるポイントを見ていきましょう。
改善を試みる際は、まず小さな点から手をつけるのが効果的です。最初から大きな改善を目指すと、実行が難しくなり、成果が出なければ意欲も低下してしまいます。
そのため、はじめは小さな改善に取り組み、成功体験を積みながら、徐々に大きな成果を目指しましょう。目に見えて効果が現れると、従業員も取り組みに前向きになり、さらなるアイデアも集まりやすくなるかもしれません。
効率化を目指す際は、単に現状の改善を目的にするのではなく、どのような結果を達成したいかを明確にすることが大切です。例えば、生産性の向上や作業環境の改善など、目標を具体的に設定することにより、取り組むべき課題や実施する施策も見えてきます。
また、改善策の数を増やすよりも、内容や実現の可能性を重視するほうが成果に結びつきやすいでしょう。
改善案を実施する前には、コストや作業負荷を十分に検討し、現実的かつ効果的な方法であるか見極めることが大切です。金銭的なコストや作業員への負担が大幅に増える改善策は、期待する効果を得られず、かえって効率を下げる恐れがあります。
例えば、新しい安全カバーの取り付けたことで作業効率を下げたり、改善目的の道具配置が不便な場所になったりすると、作業員に無駄な負担がかかってしまうでしょう。
最後に、工場で製造業務効率を改善するまでの流れを分かりやすくご紹介します。
①
課題を特定する
まず、生産ラインや業務工程で発生する問題点を見つけ、その原因や及ぼす影響を徹底的に分析します。現場の作業者が日常的に感じる課題を拾い上げ、フローチャートや図解を用いながら工程を可視化し、どこで滞りが生じているかを確認しましょう。
その後は、問題の原因や影響する範囲を詳しく分析し、実際に現場の業務にどのような影響を与えているのか把握することが大切です。
②
改善案の実施
改善案を実施する際は、まず情報収集やアイデアの企画を行い、改善策のアイデアを幅広く集めます。次に、集めたアイデアの効果や実現性を評価し、優先順位をつけて実行する改善案を選定しましょう。
その際、改善案が現行の業務工程や生産ラインにどのような影響を与えるかも考慮し、もし影響が大きい場合は対策を講じることが大切です。業務や納期に支障をきたさないように調整しながら、改善案を円滑に進めていく体制を整えます。
③
実施後の評価やフォローアップ
改善案を実施した後は、具体的なデータや現場の観察を通じて、効果を評価することが大切です。実施後の成果を測定し、業務改善の効果が現れているか確認しましょう。
また、評価は定期的に続けていき、必要に応じて追加の改善策を施すことが求められます。1度で完璧な効果を得るのは難しいため、評価を通して新たな課題を見つけ、さらなる改善に取り組むことが業務の効率化につながります。
製造業務の効率化・改善は、日々の小さな改善が大きな成果へとつながる大切な取り組みです。業務の質を高め、生産性を向上させるためにも、現場で業務改善策を実践していきましょう。
なお、Man to Manでは製造業界での幅広い求人を豊富に掲載しています。製造業界でスキルを磨きたい方は、ぜひMan to Manの求人情報をチェックしてみてください。